Refractories for Iron & Steel Industries
Today, steel is produced by two main industrial production methods. The integrated route utilises iron ore and coal in a blast furnace to produce molten iron which is subsequently transferred to the basic oxygen furnace (BOF) in which it is converted to steel. The second steelmaking route melts scrap steel and/or sponge iron from direct reduction in an electric arc furnace (EAF). KONREF provides high grade and reliable refractory materials to steel producers for their indispensible needs in the steel production.
Konya refractories is a full-range refractory manufacturer for Electric Arc Furnace (EAF), Basic Oxygen Furnace (BOF), TUNDISH, Induction Furnaces, TORPEDO Ladle, and Treatment Ladle.
For more info download Product Catalog for the Iron&Steel IndustriesElectric Arc Furnace
Electric Arc Furnace (EAF) is a steel making furnace, in which steel scrap is heated and melted by heat of electric arcs between the furnace electrodes and the metal bath.
Refractory linings of EAFs are made generally of fired magnesia and resin-bonded magnesia-carbon bricks. Fused magnesia grains and flake graphite are used as raw materials.
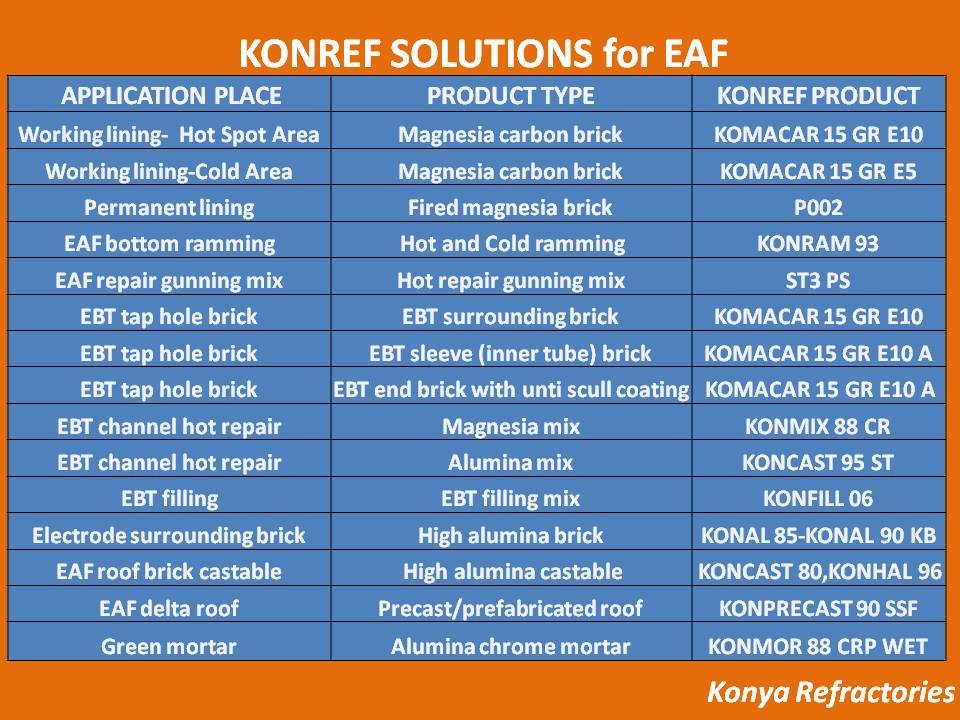
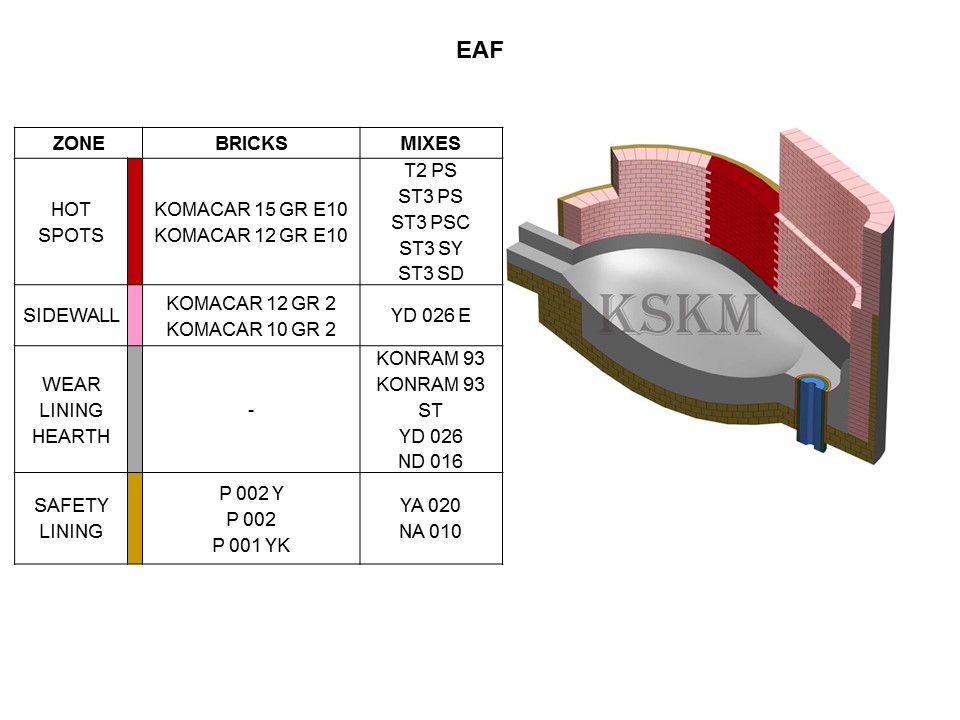
Basic Oxygen Furnace Converter
Basic oxygen steelmaking (BOS, BOP, BOF, or OSM), is a method of primary steelmaking in which carbon-rich molten pig iron is made into steel. Blowing oxygen through molten pig iron lowers the carbon content of the alloy and changes it into low-carbon steel. The process is known as basic because fluxes of burnt lime or dolomite, which are chemical bases, are added to promote the removal of impurities and protect the lining of the converter.
Refractory linings of BOFs are made generally of fired magnesia and resin-bonded magnesia-carbon bricks. Fused magnesia grains and flake graphite are used as raw materials
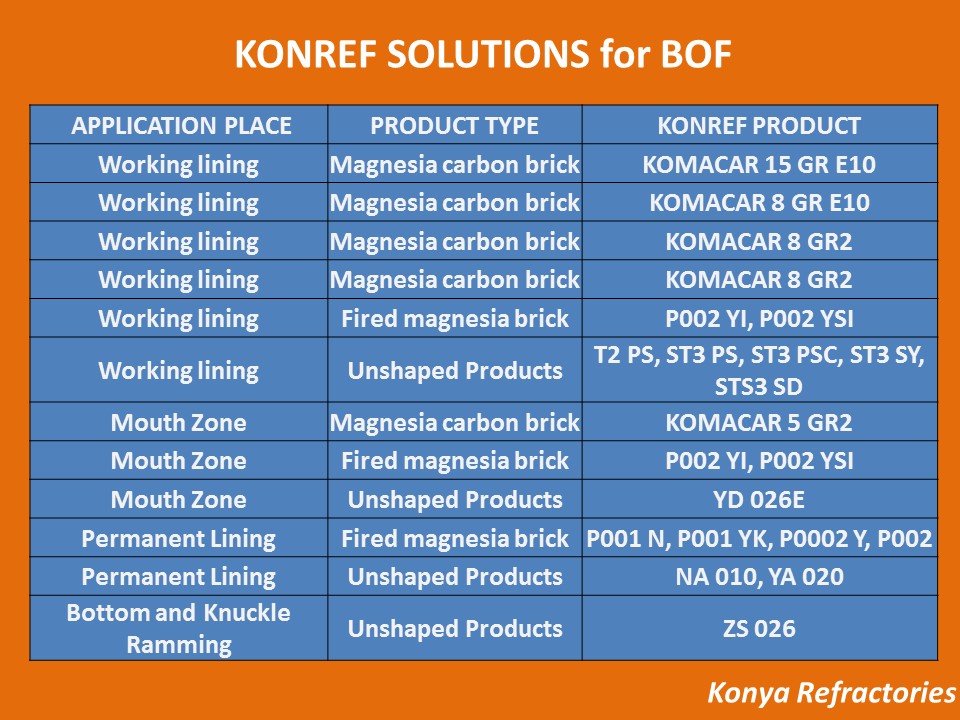
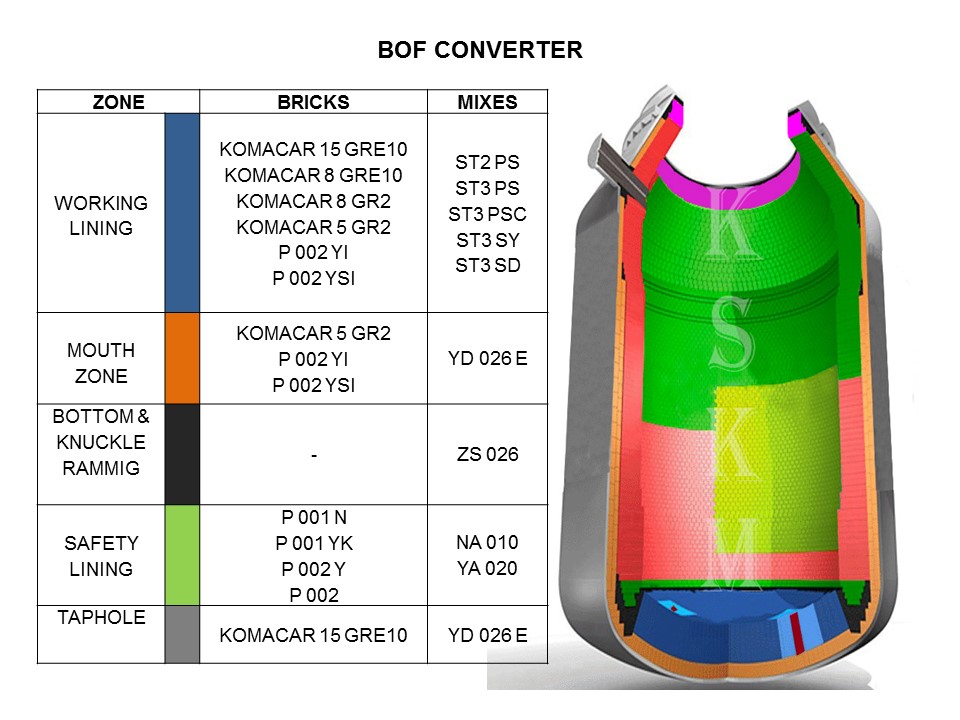
TUNDISH
A tundish is a broad, open container with one or more holes in the bottom. It is used to feed molten metal into an ingot mould so as to avoid splashing and give a smoother flow.
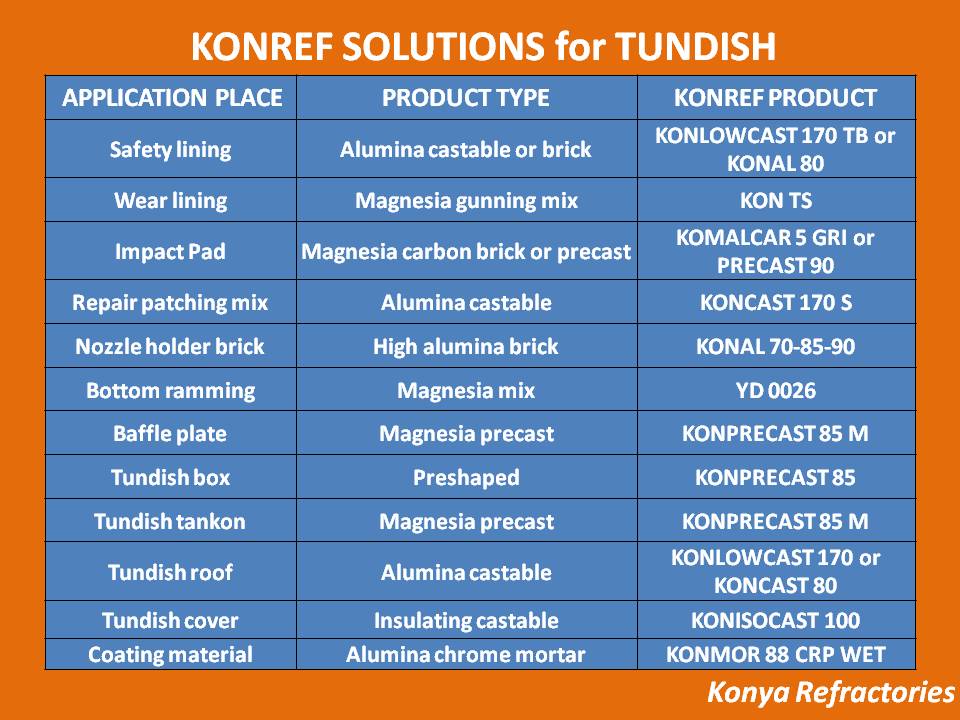
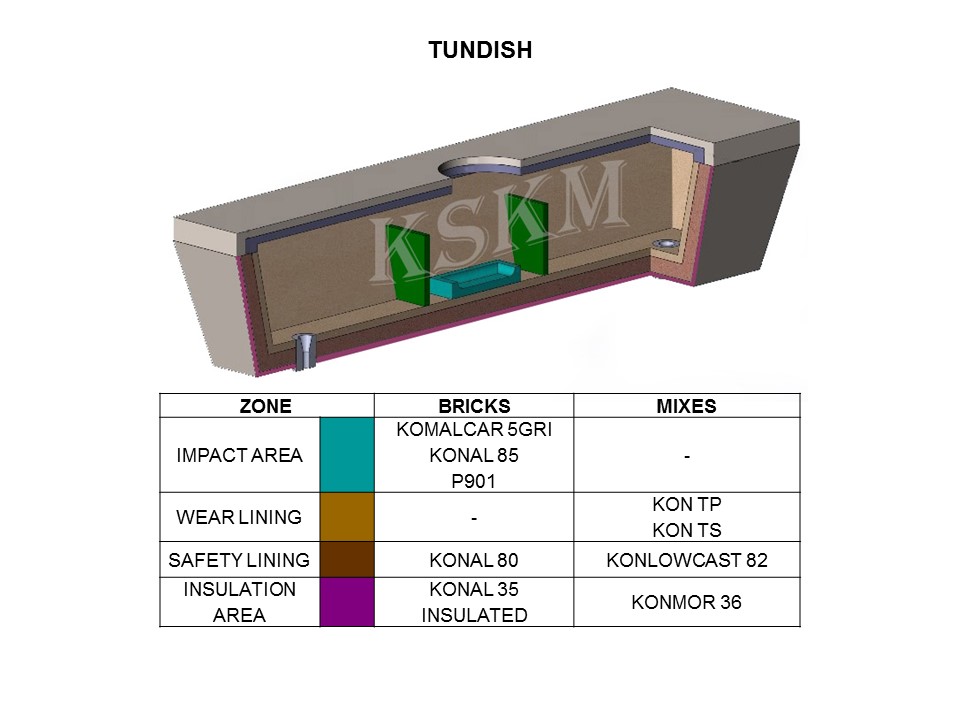
STEEL LADLE
The carrying out of metallurgical reactions in the ladle is a common practice in practically all steelmaking shops, because it is cost-efficient to operate the primary furnace as a high-speed melter and to adjust the final chemical composition and temperature of the steel after tapping.

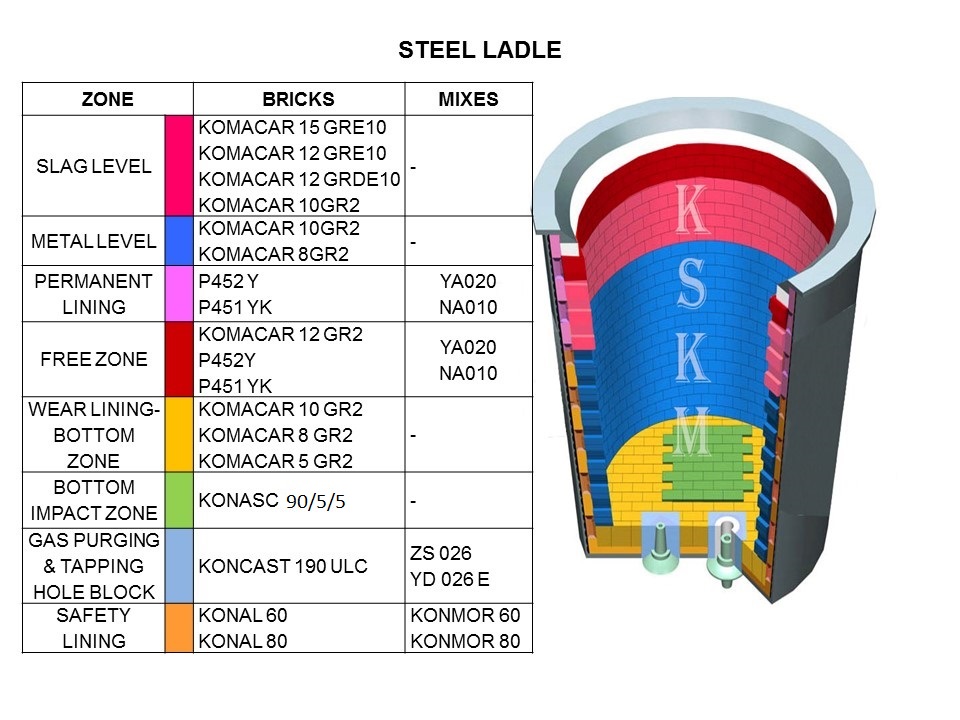
TORPEDO CAR
Torpedo ladles are commonly used to transport liquid iron from a blast furnace to another part of the steel mill.
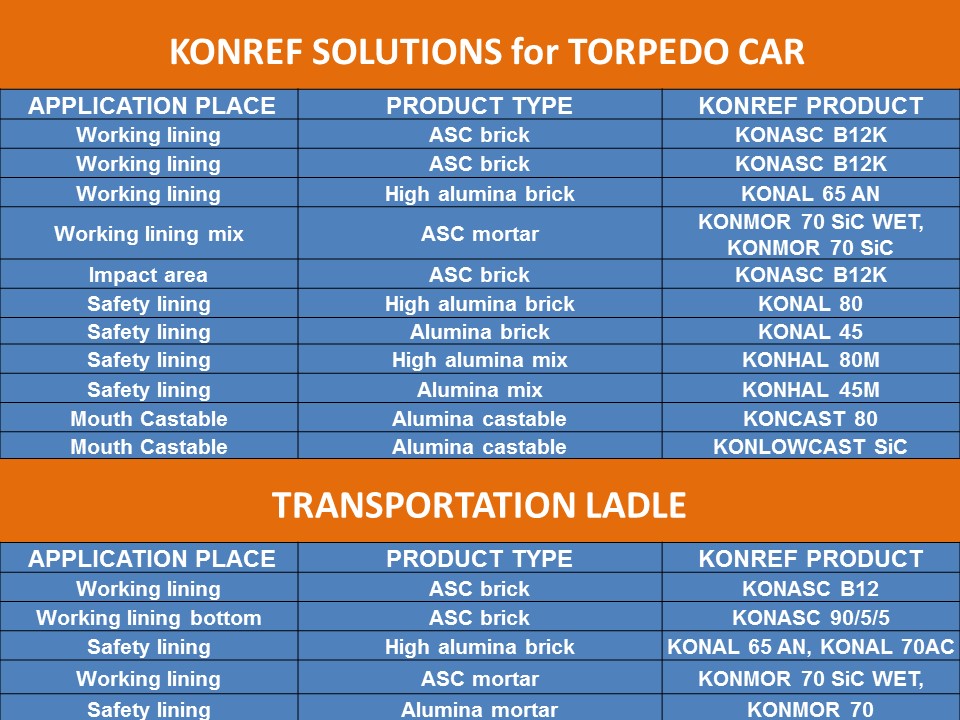
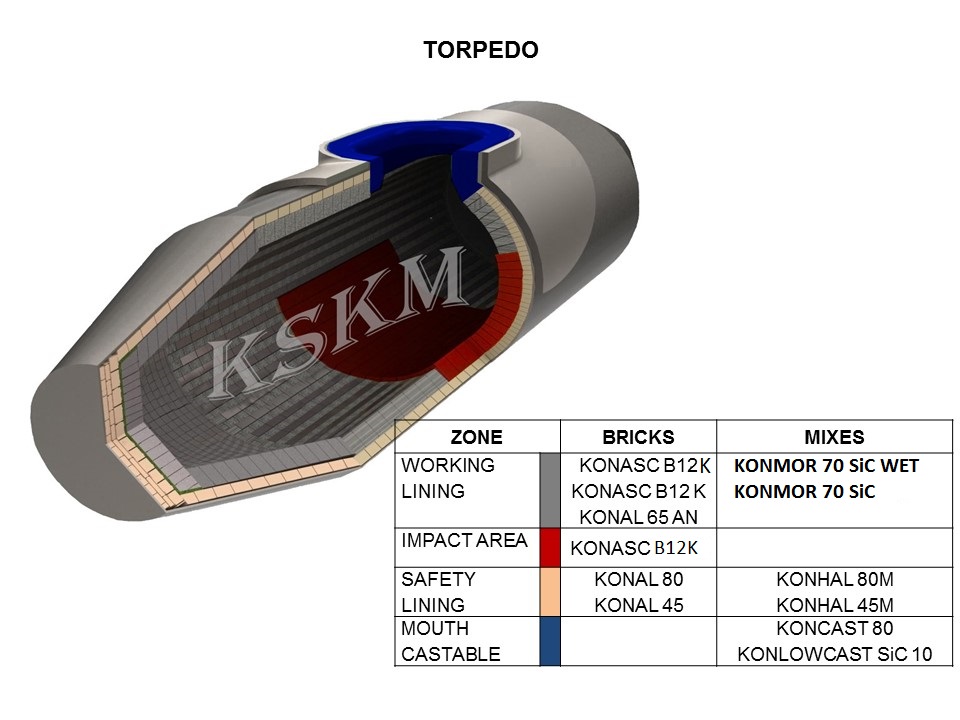
Rolling Mill Furnace
In steel plants reheating furnaces are used in hot rolling mills to heat the steel stock (Billets, blooms or slabs) to temperatures of around 1200.
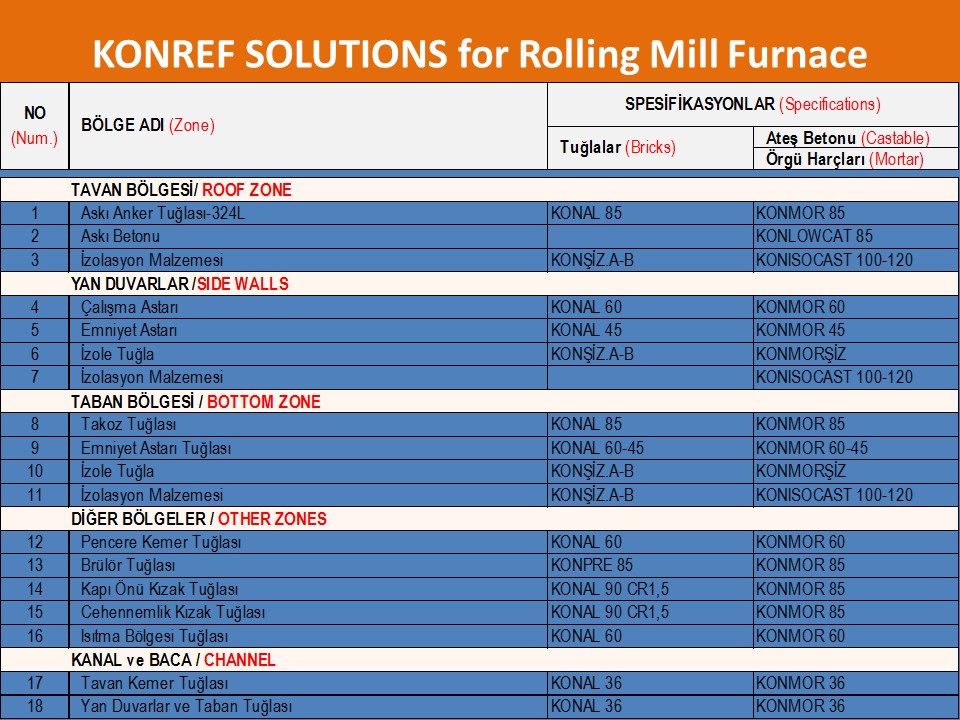
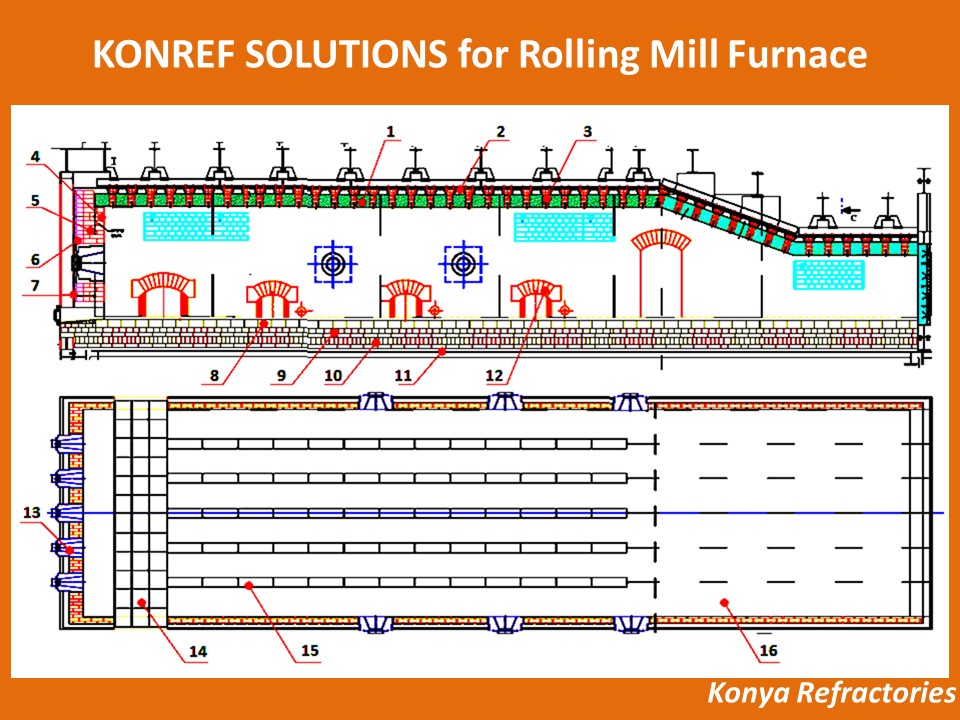
Induction Furnace
An induction furnace is an electrical furnace in which the heat is applied by induction heating of metal. Induction furnace capacities range from less than one kilogram to one hundred tonnes, and are used to melt iron and steel, copper, aluminium, and precious metals
The bottom structural part of Induction Furnace on which main crucible lies is generally lined with bricks and do not require to be changed frequently. However, working face of the main crucible is lined with a suitable ramming mass. Selection of the ramming mass(R/M) entirely depends on the scrap melted and operating parameters. The roof is lined with a suitable castable generally of High Alumina base and Low Cement Castable (LCC). The launder or spout of the furnace either is rammed or lined with refractory bricks. For side wall lining a suitable cylindrical former is essential. The former can be made either removable or consumable type. In case of consumable former the quality of the former should be compatible with the quality of the product (melt) to be produced. Generally bottom ramming is done first followed by the side wall ramming. Ramming is generally done layer-wise with the help of pneumatic rammers to ensure compaction and packing density. At the same time to avoid lamination between the layers each layer is to be scratched before putting fresh material for further ramming.
For more info download Product Catalog For Induction Furnace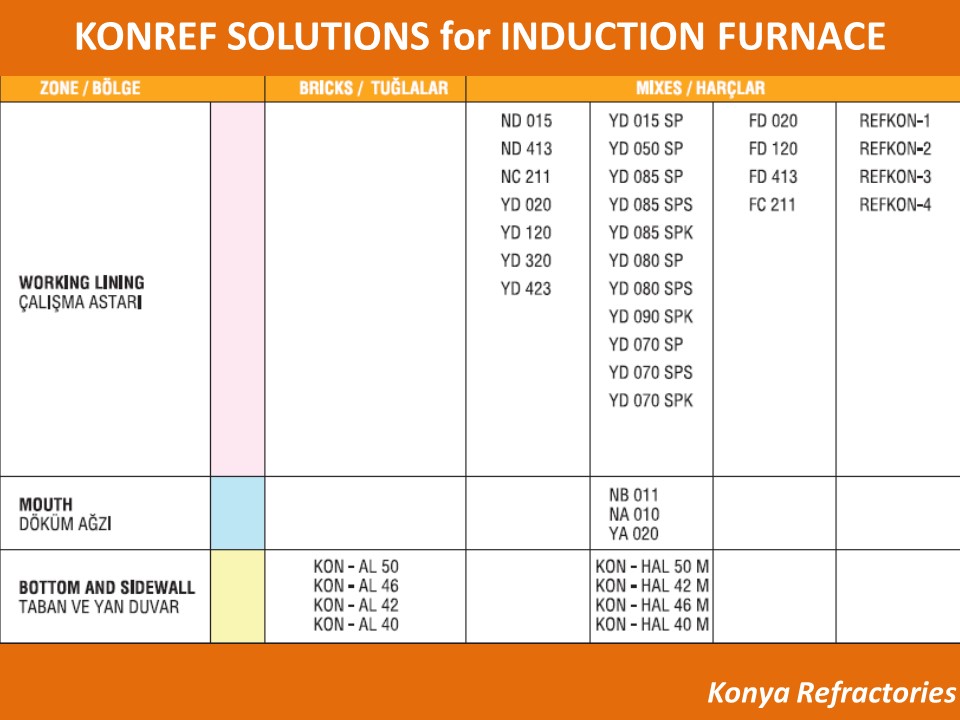
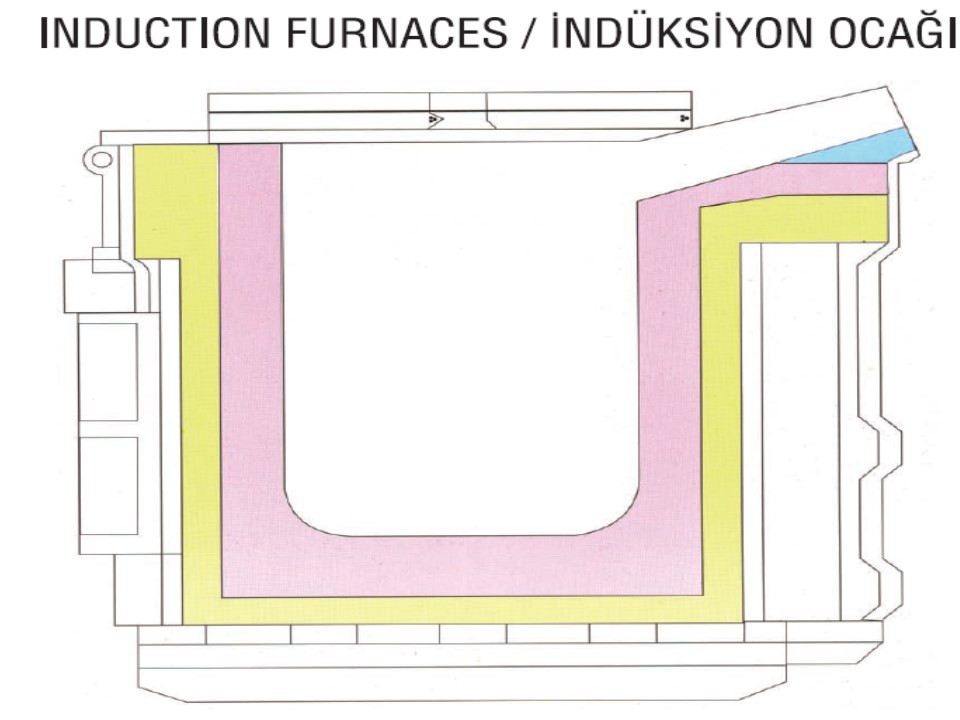
a general view of steel production;
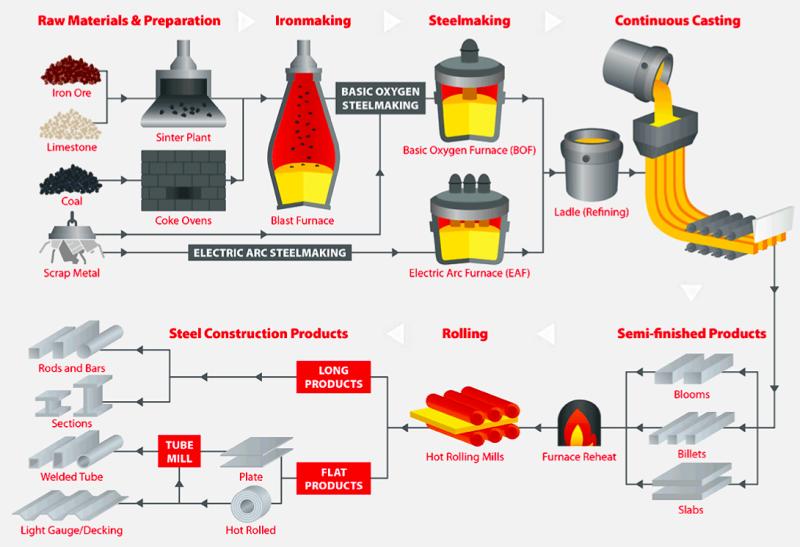